vol.2 石田一生さん
JUKI会津株式会社で、医療用具から船舶、航空機の部品まで、さまざまな金属部品の製作に携わっている石田一生さん。今回は石田さんに3Dプリンターの活用や鋳物づくりのお仕事についてお話を伺いました。
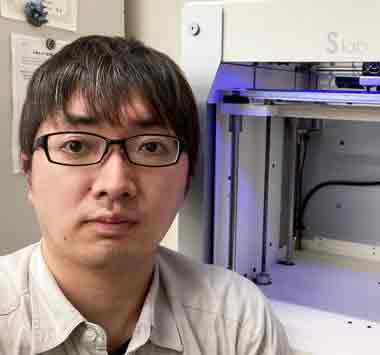
石田 一生さん
―早速ですが石田様のお勤めの会社とそこでどのようなお仕事をされているのかご紹介いただけますか?
石田さん: 私が所属しているのは、工業用ミシンのJUKIグループの一つ、JUKI会津株式会社という会社です。弊社は、ロフトワックスという鋳造品と、MIMというプラスチック成形の応用による方法で製造した金属部品をお客様へ提供しています。 私自身は技術部に所属し、お客様からご依頼いただいた製品を実際に鋳物にするまでの立ち上げや、その後量産していく上での改善を図ることをメインに、完成するまでの全ての工程に関わった業務をしています。
―お客様はどのような業界の方が多いのでしょう?
石田さん: 結構いろいろで、一般産業機械、発電所関係、人工関節の素材や理美容関係のハサミ、カミソリ、一般の方が目にするようなものも造ります。
―設計もされるのでしょうか?
石田さん: 基本的に設計はしないです。お客様から2次元図面とモデルをセットでいただき、それを鋳造用に少し肉をつけたり、図面上厳しい寸法のところに緩和を入れたりするなど直すことはあります。
― 一つの製品の製作期間はどのくらいなのでしょう?
石田さん: 注文をいただいてから2ヶ月位です。図面に落とすのは1~2週間位ですが、そこから製品のモデルを造る金型を起こし、さらに鋳込むための型を造るのに2週間位かかったりするので。
―子供のころからものづくりに興味があったのでしょうか?
石田さん: そうですね、昔からものづくりに興味がありました。大学は南部鉄器が有名な岩手で、学生時代はその南部鉄器など砂型の鋳物について勉強しました。ご縁があって今の会社に入り、異なる鋳造方法で鋳込んだものを造っています。
―お好きな事を仕事にされたのですね。3Dプリンターは、具体的にどのようなところで使われているのでしょうか?
石田さん: 弊社では、鋳型を造る前に1回、ロウ(ワックス)で製品のモデルを造るのですが、そのための金型の製作で1ヶ月位かかることがあります。短納期で試作をする場合、その金型の製作期間を省くために3Dプリンターで直接、製品のモデルを製作します。3Dプリンターだと1~2日で造れてしまうので。 また、そもそも1回の発注が2~3個で、リピート注文がない案件もあります。そういう時も金型を起こすと値段が高いので、3Dプリンターを使用したほうが早く、値段も安くなり、お客様にも喜ばれます。 その他に使うのは、鋳造する上で必要な部品、例えば溶けた金属の流れ道を作るための部品を作るための金型や治具などです。金属でいちいち削って造ると高くなるので、簡単な型であれば、型そのものを3Dプリンターで造ることもあります。
―3Dプリンターを使いこなすように覚えるのは大変でしたか?
石田さん: う~ん、大変ですが、結構楽しみながら勉強しました。インターネットで造形条件の設定を調べたり、今回受けた検定で勉強しました。試行錯誤しながら独学ですね。 また、プラスチックを造形する上でどのくらいの温度が良いとか、プラスチックの特性に詳しい人に聞きながら条件をいじったりしています。
―3Dプリンターの条件は素材に詳しい方が良いのですか?
石田さん: はい、同じメーカーの素材でも、色によっても若干特性が違うので、やりながら条件を変えたりしています。
―3Dプリンターを使ったお仕事で楽しいと思う時はどんな時でしょう。
石田さん: コンピュータ上で作ったモデルが、3Dプリンターで造形されて実際に手に取る形になった時は楽しいな、と思います。 また、素材の色によっても条件が異なるので、仕事で使うものを綺麗に造形するために簡単な形のもので条件だしを確認するのですが、その時に仕事に関係のない、例えばアニメのキャラクターを造って楽しんでいます。
―楽しみながら3Dプリンターを使われているのですね。これまで難しくて投げ出したくなるようなことはありましたか?
石田さん: そうですね。鋳物自体の難易度が高いものもあったのですが、納期がシビアなものがありました。何月何日に出港する船に乗せなければいけないので、絶対にこの日までに品物をあげてください、という案件です。その時には、その品物だけに注力してなんとか間に合わせました。難易度もそうですが納期のプレッシャーがあります。
―厳しいお仕事ですね。逆に、仕事をされていて良かったと思う時はどんな時ですか?
石田さん: お客様に試作したものを持って行き、難易度が高かった部分について「よく造ってくれた」とお誉めいただいた時は、やりがいがあったと思います。 また、設計時の打ち合わせでは、製造する部品を使う用途として、様々な業界の最新の開発案件の話を聞く機会があります。発電所もそうですし、ロケット、航空機、深海探査船など、日本の科学技術分野の最新の案件の話を聞けるのも楽しいです。
―仕事で求められる知識やスキルはありますか?
石田さん: 鋳造の知識はもちろんですが、お客様に提案する上で、製品の専門分野の負荷強度や加工についての知識。航空機なら航空機の知識をある程度身につけておくことが必要です。機能を確保しつつ、でも鋳造ではこうした方が良いという話をするために、いろんなジャンルの知識を身につけるようにしています。
―多岐にわたる分野を手がけていらっしゃるので大変ですね。今後やりたいことや抱負などありましたら教えてください
石田さん: 今、弊社で重点的に取り組もうと思っているのですが、さらに3Dプリンターの技術を活用して社内の効率アップや、お客様に対して新しいビジネスの形態を提案できないかと考えています。 一つは、金属3Dプリンターの技術を応用して、砂をのりで固めることによる造形方法で、金属を鋳込む時に使う鋳型を造ること。 また、弊社ではプラスチック射出成形の技術を使っていますが、そちらに関しても金属粉末とプラスチック粉末を混ぜたフィラメントをFDM方式の3Dプリンターで造形することで、MIMと3Dプリンター の技術をコラボさせた金属部品を造りたいと考えています。 すでにテストに着手しており、今年度中には終える予定です。上手くいったら、それをどういう形でお客様のビジネスに役立ててもらえるか、どういう形で提案していくかを考えていこうと思っています。
―3Dプリンターを活用した新しいビジネスにチャレンジされているのですね!最後に、3Dプリンター活用技術検定についてお聞かせください。どのようなきっかけで受験されたのでしょうか?
石田さん: 3Dプリンターを使い始めるのに当たって、ちゃんと勉強しておきたいと思い資格がないかと調べて受験しました。
―受けてみていかがでしたか?
石田さん: 非常に勉強になりました。今までは独学で自社の3Dプリンターの使い方だけしか知らなかったのですが、その他の造形方法や、それぞれの造形方式の利点、欠点を学べたのが良かったです。 また、弊社は鋳造で部品を造っていますが、金属3Dプリンターがライバルになるのではないかと、同業他者とも話していました。今までは知識がなく漠然と危機感をもっていたのですが、今回きちんと学んだことにより、金属3Dプリンターと鋳造、それぞれのメリットとデメリットがわかりました。まだまだ鋳造も大丈夫だと改めて認識できて良かったです。
お客様のために鋳物を造りながら、3Dプリンターの可能性を拡げるために新しい製造方法を研究・開発されている石田さん。難しいことも多いけれど、ものづくりの仕事はやりがいがあり楽しいと話されていました。お忙しいところインタビューにご協力ありがとうございました。